It may feel intimidating at first to do this yourself, but with a few trials it is relatively easy.
sriad84 recently shared this with other BHPians.
As promised, here is the carbon fiber lamination DIY details. As you may already know, I have laminated Saya (my Continental GT650) in carbon fiber. It may feel intimidating at first to do this yourself, but with a few trials it is relatively easy (in some ways easier than vinyl wrapping, but that's just my personal opinion).
Why lamination and not full carbon fiber?
- If all you want is a cosmetic improvement (no weight savings). Infact, you would add a little weight (fabric + resin)
- It is real carbon fiber and unique (at least for a RE)
- Relatively inexpensive (not considering the time you would spend to do this)
What you will need
- Carbon fiber fabric - Choose the weave pattern you would like. Some of the most common patterns are - plain weave, twil (2X2 or 4X4) weave and Harness Satin weave. I went with 2x2 twil as it was easily available locally.
- 3M 77 Super Multipurpose Adhesive Aerosol.
- Clear, low viscosity, UV resistance (no yellowing) epoxy resin + hardener
- Black spray paint
- Sand paper (wet and dry) - 400 to 2000 grit
- Masking tape (3M or good quality ones)
- Small wooden hanging clips (backup)
- Electronic scale to measure the resin/hardener mix
- Soft bristle, good quality (1 to 2 inch wide) paint brushes (3-5) - New brush for each coat as the resin hardens and renders it useless for next use.
- Dremel or similar tool for finishing
- Exacto knife & scissors
- Latex gloves
- Enough workable space indoors which is dust free (spare bedroom in my case )
- Rag/newspaper/cloth to lay on the floor
- Clear coat - recommend professional shop for best results
Helpful links to get carbon fiber and resin (this is what I used, you may find other sources)
The process (I will use the motorcycle tank, front fairing and tail as references here)
Step 1 : Understand the amount of material you will need
- Carbon fiber fabric from where I sourced came in 1m wide roll and you can order as many meters in length as you want. Lay the parts down and get a rough idea of square footage. If you are OCD like me, make sure you are considering the direction of weave to match on all panels. I got 1m x 5m fabric. Extra is always better as you wont get it right the first time (or maybe you will).
- Epoxy resin - I used 3 kg total and probably have some 250 gm left over. 3-4 coats and rework and there will be wastage as it drips after application.
- Generic black spray can - 1 to 2 depending on the surface you need to cover (you will see why in later steps).
Step 2: Prep the parts for lamination
- Clean parts thoroughly and sand it down a little (better adhesion)
- If you have a base color which is lighter shade or anything other than black, I recommend spraying a coat of black color (I preferred matt). The reason to do this is as you lay the fiber, the weave will move a little and show what's behind. Painting black will make it hard to notice and you will thank me for it. Re-sand post painting if required
Step 3: Cut the required fabric
- When doing so, please mark an outline and tape the outline with masking tape and cut in the middle of the tape. This ensures the fabric stays together. If you cut without doing this, the weave will come off and turns into a nightmare. Learnt the hard way!
- Caution - please ensure the fiber particles are cleaned immediately as they can splinter, especially if you have toddlers at home.
Step 4: Laying the fiber on the part. There are two ways to get the fiber to stick to the base metal/plastic
- Option 1: 3M aerosol glue - works great and easy to spray on evenly. But depending on type of resin you use, the glue will dissolve while applying resin later and there would be a risk of fiber lifting from the base surface. To avoid this, you can use the clips I mentioned in the list on the edges of the part to keep the fiber in place during resin process, also can use masking tape on the insides of the part (after you fold carbon fiber over) over the fiber material to keep it in place. Surprisingly masking tape does not come up when resin is applied. Leave parts for few hours to let it set well.
- Option 2: Use the resin/hardener mix itself to paint brush a thin layer on the part and then lay the fiber. You have more time with this method as the setting time for resin is higher unlike 3M and gives you some time for adjustability/re-placement. Leave parts for curing time or at least dry to touch (can be anywhere between 8 to 24 hrs).
Pictures of the tank post the laying of the fiber. Sorry I did not take pictures of the previous steps when I did this.
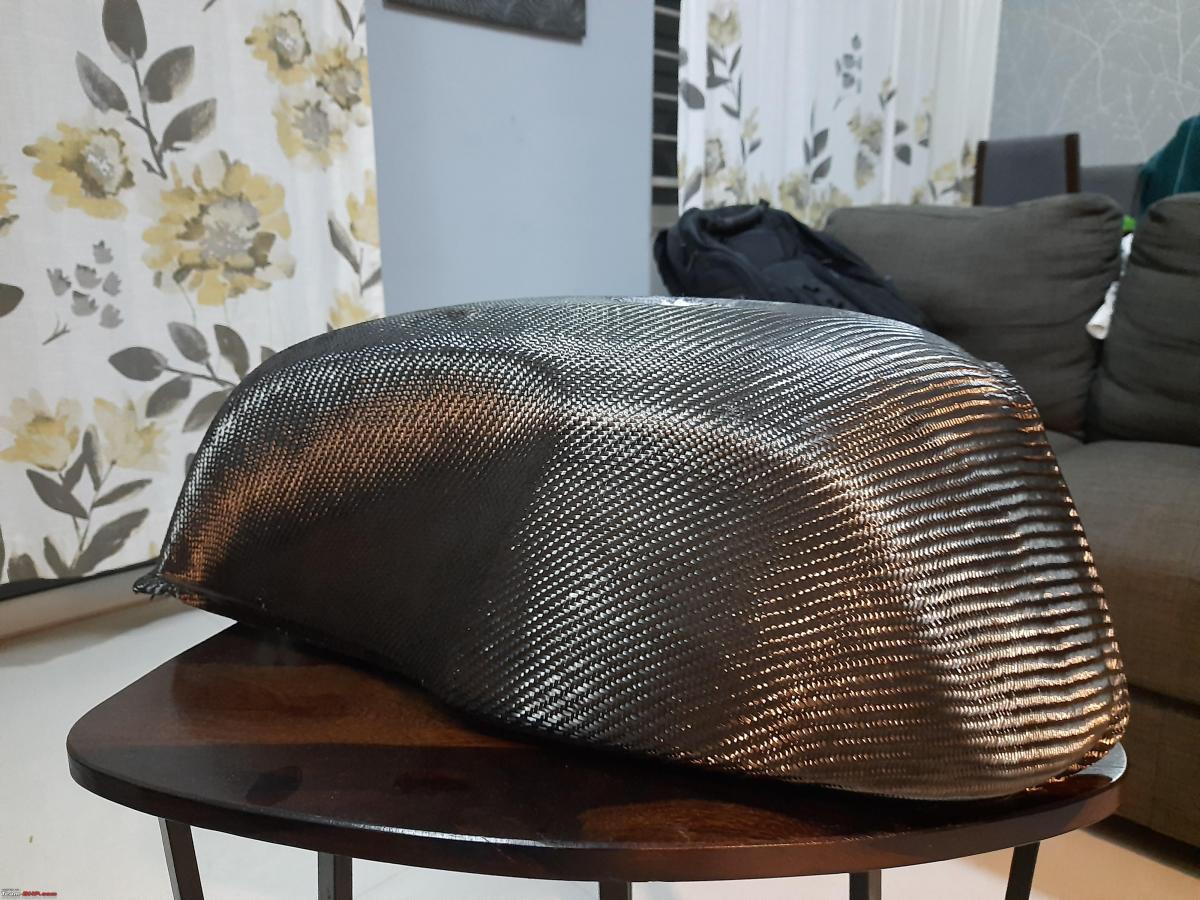
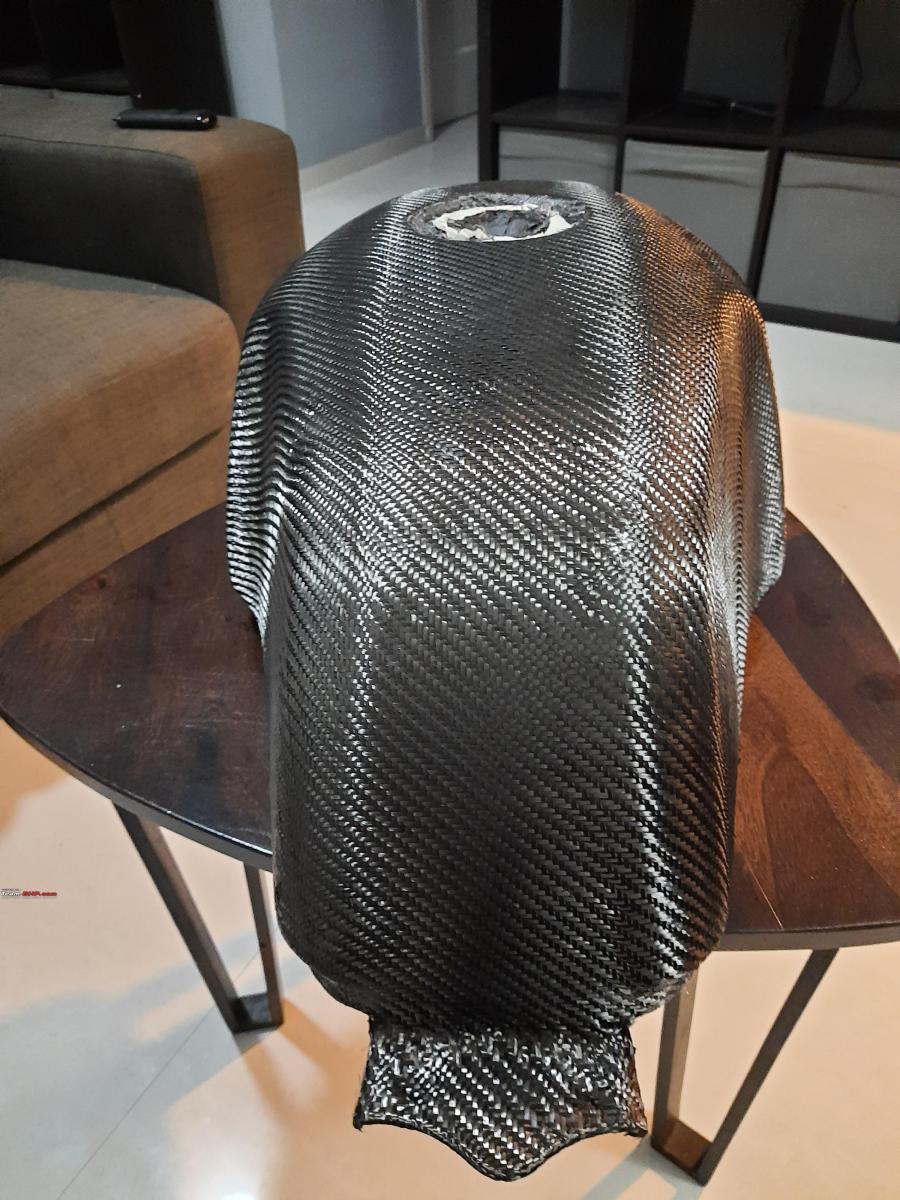
Step 5: Applying the epoxy resin
- Ensure you have sufficient time. Recommend 3 to 4 coats of resin application and time between each coat is 3-4 hrs. Resin should still be wet when applying another coat, do not let it set.
- Most epoxy resins need to be mixed in 2:1 ratio (resin : hardener) by weight and not volume. So be careful when doing this. Best is to use a kitchen scale and mix small quantities at a time. For the tank, for a single coat, I used 100g resin and 50g hardener. Mix this well using an ice-cream stick or the paint brush or whatever works. Try to avoid bubbles while mixing.
- Use the paint brush to apply even coats across the surface evenly. Generous application is ok, but avoid resin from pooling in areas where it may collect (in my case near the tank filler hole). Thin consistent layers and multiple layers will give best results. Keep an eye for bubbles and run the brush over that region to pop them. You do not want bubbles from getting trapped while setting.
- Repeat the above step 3 to 4 times at an interval of 3 to 4 hrs between each coat. Once done, let the parts set for 24 hours (check curing time for the resin you are using, be patient).
Pictures of the front fairing and tail during the resin application shown below. Where the shape did not allow for one piece of fabric to be laid, I kept the joints where I knew I would be painting over.


Pictures of the set parts before sanding
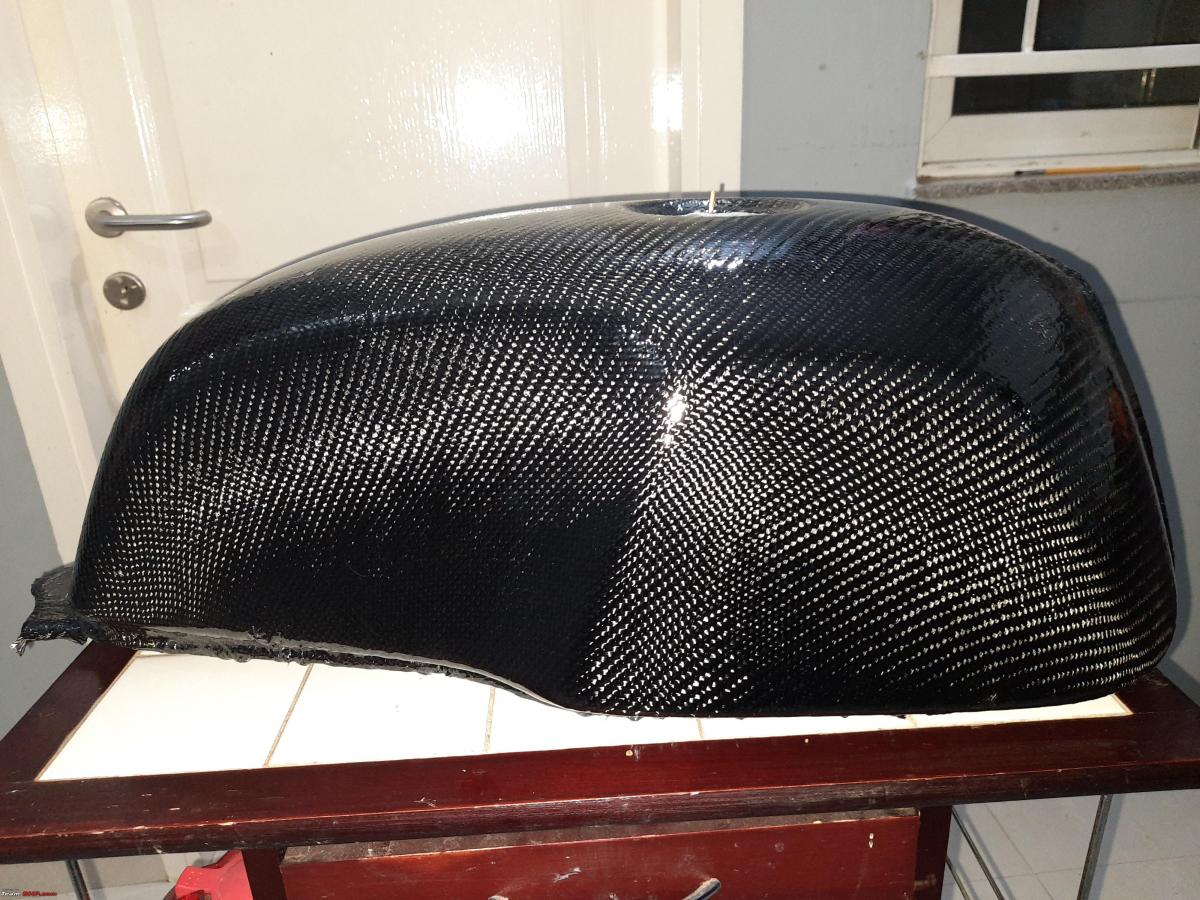
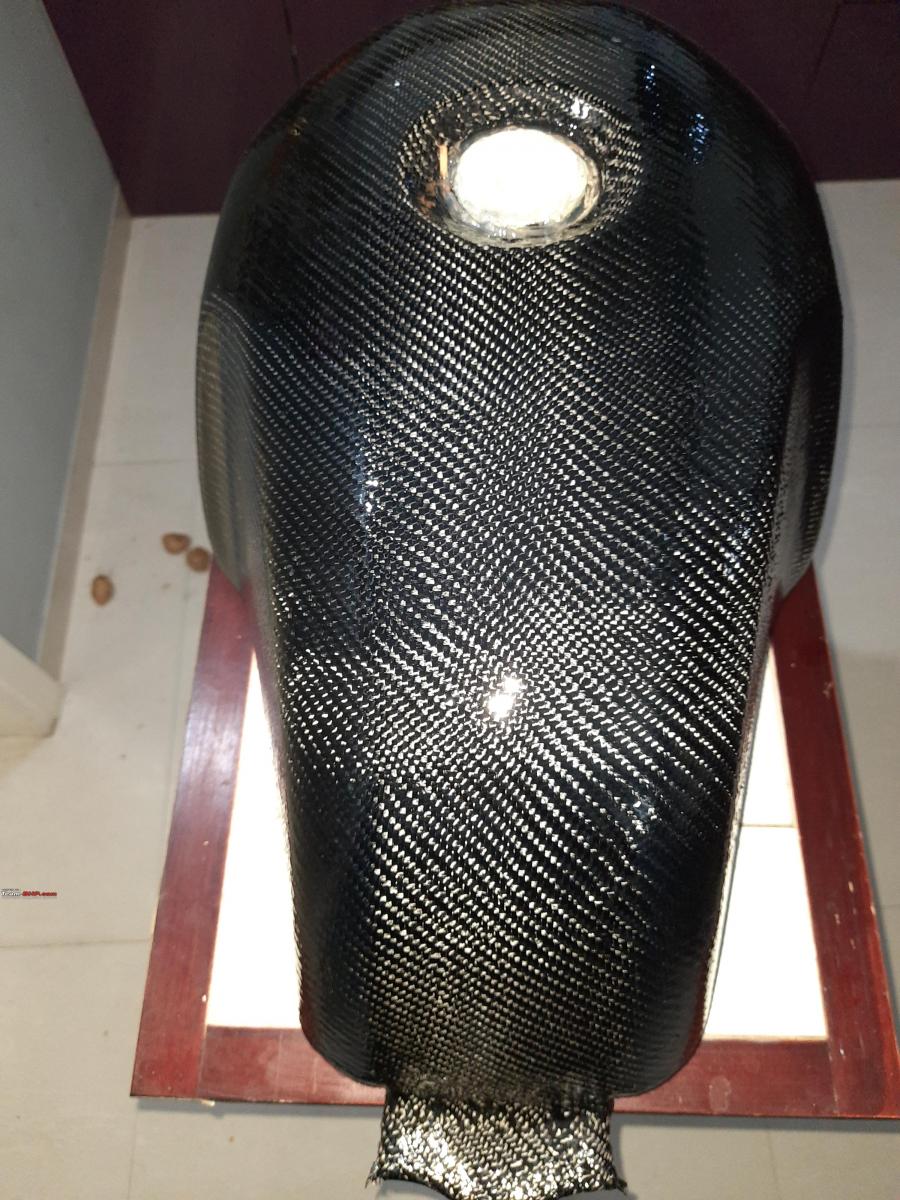
Step 6: Finishing - wet sanding
I started with 400 grit and worked my way up to 2000 grit for a smooth finish. Resin will lose shin and translucency after this stage. Be careful not to overdo this as it takes the resin layer too far down. Some pictures post sanding while doing some mock ups for paint ideas.
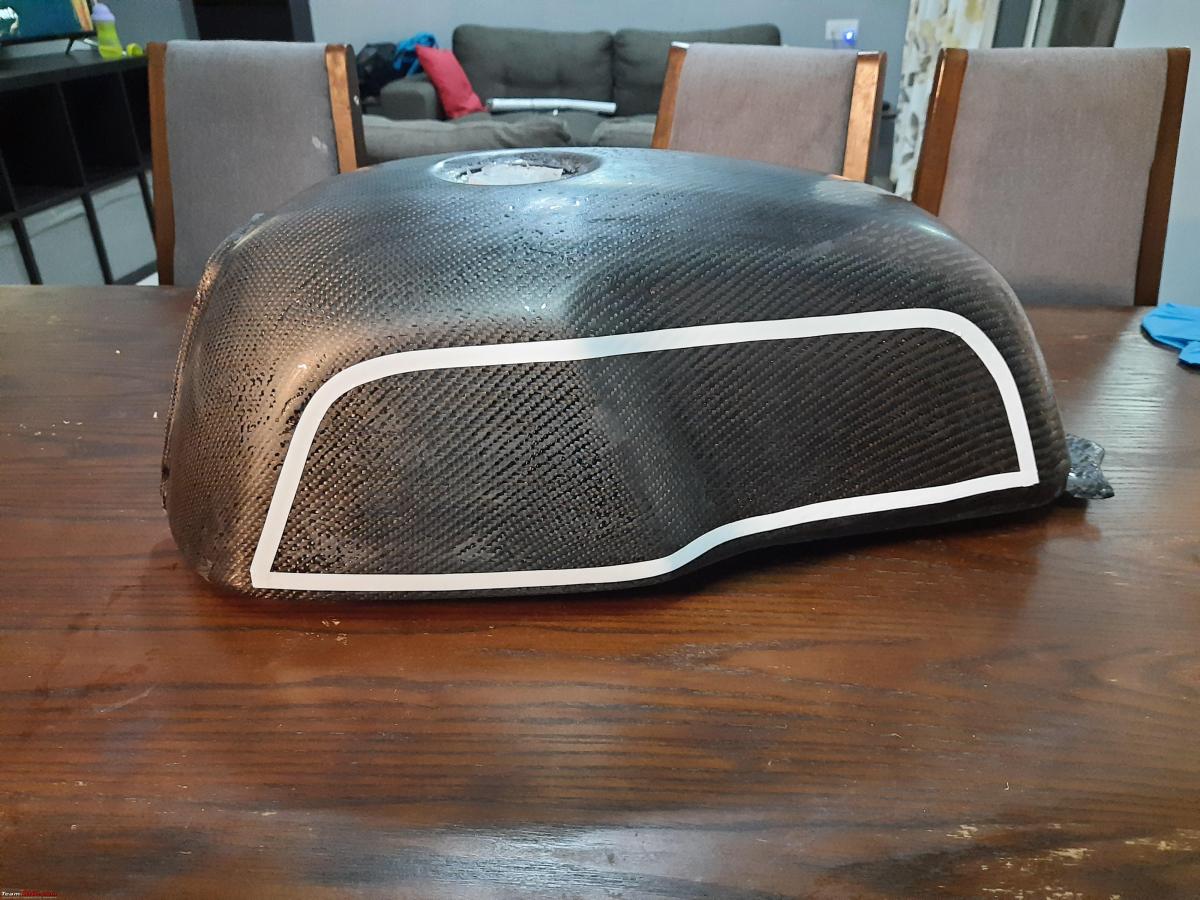

Step 7:
Final prep and clear, finished product (done by Ricochet Motorcycles).
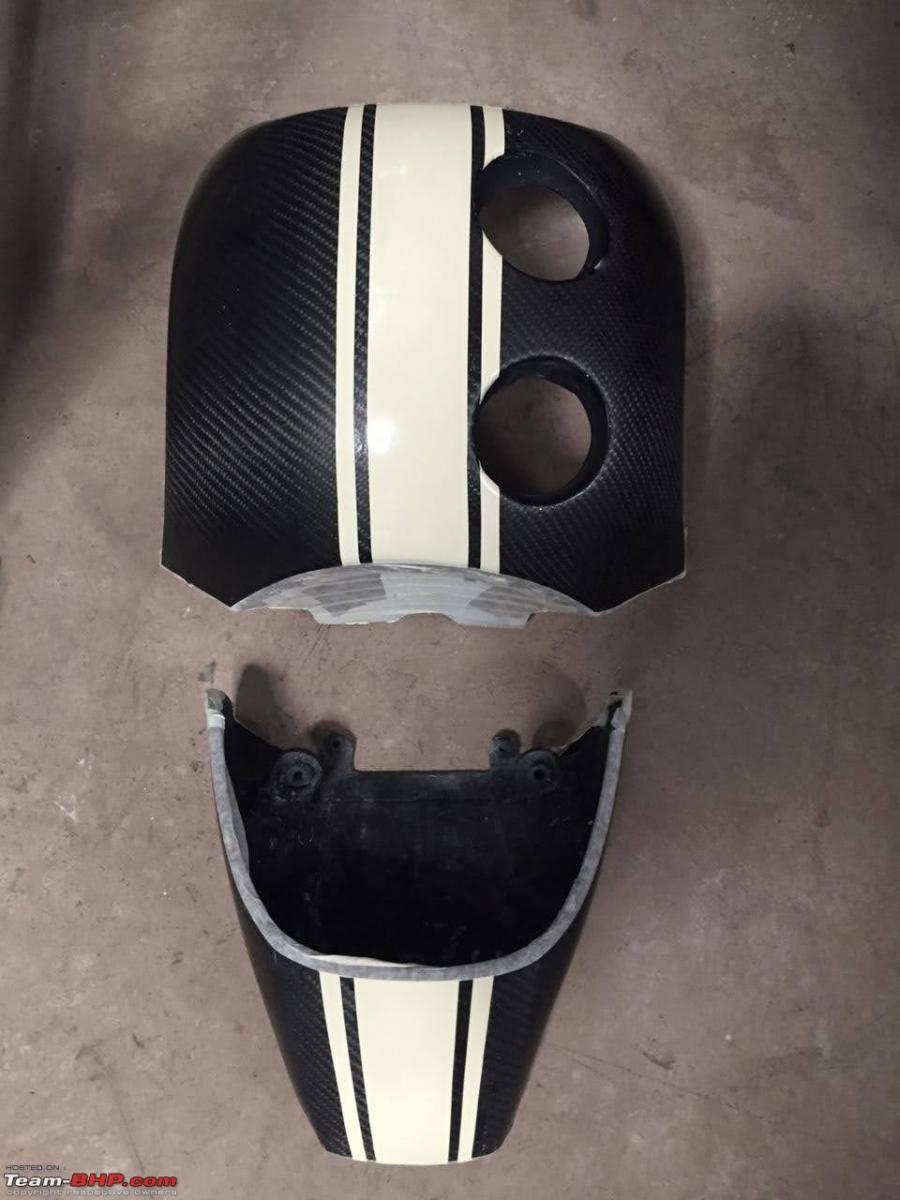
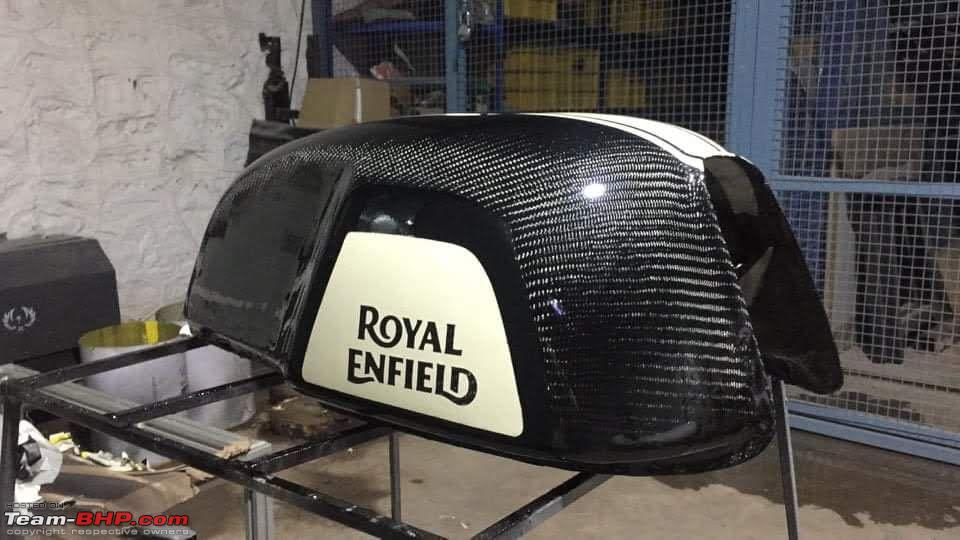
Hope this helps!
Thanks to sriad84 once again! Check out BHPian comments for more insights & information.