Quote:
Originally Posted by dhanushs Thanks for the reply Aroy. The last 3 clutch plates of mine, have shown the same problem.
What do you suggest about using a non spring type hub? Yes, GB will take a hit when I dump the clutch, but again, would appreciate your take. |
See if you can get clutch plates with better springs. May be some truck's clutch may be same size.
Here is how the clutch plate functions
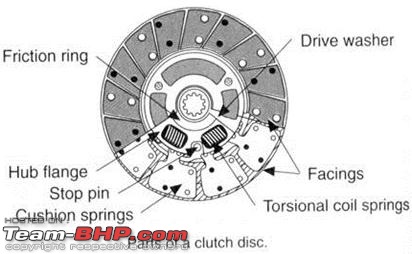
"Among the numerous criteria used to determine clutch size and clamp load configuration, maximum engine torque and the resulting friction energy are especially significant. The greater the clamp load, the smaller the friction radius can be. The diameter should be as small as possible, because it greatly affects clutch weight and cost. But the clutch disc also has to be large enough to handle thermal loads and facing wear.
The clutch disc, also called friction lining, consists of a splined hub and a round metal plate covered with friction material (lining). The splines in the center of the clutch disc mesh with the splines on the input shaft of the manual transmission. This makes the input shaft and disc turn together. However, the disc is free to slide back and forth on the shaft.
Clutch disc torsion springs, also termed damping springs, absorb some of the vibration and shock produced by clutch engagement. They are small coil springs located between the clutch disc splined hub and the friction disc assembly. When the clutch is engaged, the pressure plate jams the stationary disc against the spinning flywheel. The torsion springs compress and soften, as the disc first begins to turn with the flywheel.
Clutch disc facing springs, also called the cushioning springs, are flat metal springs located under the friction lining of the disc. These springs have a slight wave or curve, allowing the lining to flex inward slightly during initial engagement. This also allows for smooth engagement.
The clutch disc friction material, also called disc lining or facing, is made of heat-resistant asbestos, cotton fibers, and copper wires woven or molded together. Grooves are cut into the friction material to aid cooling and release of the clutch disc. Rivets are used to bond the friction material to both sides of the metal body of the disc.
Most clutch facing have a base of asbestos. The number of friction surfaces is equal to twice the number of driven discs.
Large driven plates have a tendency to spin (i.e. to continue rotating after the clutch pedal is depressed). To limit this trouble, the plate should be made as light as possible.)
A material suitable for use as a friction surface must meet the following conditions:
- It must have a high coefficient of friction
- It must not be affected by moisture and oil
- It must resist wear
- It must be capable of resisting high temperatures caused by slippages
- It must be capable of resisting high axial pressure
- should have the given rapture strength,
Note that,
* There are groves in both sides of the friction-disc facings. These grooves prevent the facings from sticking to the flywheel face and pressure plate when the clutch is released. The groves break any vacuum that might form and cause the facing to stick to the flywheel or pressure plate.
** The facing or lining on the driven plate are secured by brass rivets, the heads being recessed into the lining to prevent scoring of the flywheel and pressure plate faces. As the lining wear down, the inner ends of the release leaver move away from the flywheel and after a predetermined a mount of wear has taken place; the lever will touch the cover.
Cushioning plate (center plate):
The cushioning plate, on which the friction facing are mounted, consists so series of cushion springs which is crimped radially.
During engagement, axial compression of the driven plate spreads the engagement over a great range of pedal travel and therefore makes it easier to make a smooth engagement.
During the disengagement, when the pedal is depressed, the clamping force will be released and the plate springs return back to its original position crimped (wavy) state, and that will get the driven plate to jump away from the flywheel to give ‘clear’ disengagement. While in this position, the linings will be held apart, and air will be pumped between the linings to take away the heat.
This plate is also slotted so that the heat generated does not cause distortion that would be liable to occur if it were a plain plate. This plate is of course thin to keep rotational inertia to a minimum.
Driven plate torsion springs:
The plate and its hub are entirely separate components, the drive being transmitted from one to the other through coil springs interposed between them. These springs are carried within rectangular holes or slots in the hub and plate and arranged with their axes aligned appropriately for transmitting the drive. These dampening springs are heavy coil springs set in a circle around the hub. The hub is driven through these springs. They help to smooth out the torsional vibration (the power pulses from the engine) so that the power flow to the transmission is smooth.
In a simple design all the springs may be identical, but in more sophisticated designs they are arranged in pairs located diametrically opposite, each pair having a different rate and different end clearances or using dual springs, where a smaller spring inside the original one.
The role of dual spring is progressively providing increasing spring rate to cater to wider torsional damping. Also, to avoid “plate float” which could happened when using identical springs with same rate (stiffness), plate float will happen if the vibration and torque variation became equal to the natural (resonance) frequency of the spring. Plate float will have negative effect on the transmission gears (gear rattling).
Driven plate torsional dampers:
It consists of friction plate and washer, to reduce gear rattling. The friction between the friction plate and the washer will damp the torsional vibration (as the roll of shock absorber in the car suspension).
http://www.thecartech.com/subjects/a...uto_Clutch.htm
One workaround is to cool the clutch adequately. If possible you can use a blower to force cold air into the bell housing, that will cool the clutch when used aggressively.