This is my first thread on TBHP after years of being an outsider and then limited participation on various threads.
I have a 2010 Fortuner (maybe I'll put up an ownership thread some day) with 167,xxx kms on the odometer. I've owned it from 2016 when it had done 99,666 kms.
About me
I have an OCD for mechanical/engineering perfection and this attribute has not let me down in life to date. This isn't the first old car in my life. I've grown up old with Ambasaddors and not afraid of regular breakdowns. My first car was a 3rd owner, 7 year old 1997 Maruti 800 that had everything broken when I bought it. I kept it for 5 years and sold it in ship shape. It could outrun my friend's MPFI Maruti 800.
The issue
I had been planning a replacement of injectors since they were about 14 years old. Not that there were issues with pickup or smoke but I still wanted to do it with a hidden agenda to add a Quantum stage 1 tune. I already run a Denso refurbished common rail fuel pump and my 1KD Fortuner does redline aroud 4K RPMs. It is on a strict diet of
XtraGreen (IndianOil rolls out green fuel "XtraGreen" at 126 Fuel Stations across 63 cities in India) diesel since it launched in 2021.
Toyota had introduced an injector refurbishment program along with Denso in the past and it was designed to keep the total cost of ownership of Toyota diesels low. A new 1KD injector costs about Rs. 50,000.
I had some time in February 2024 and decided to send the car to Nandi Toyota to get the injectors replaced and sort out some other issues. I've been a customer of Nandi Toyota for the last 8 years and have shared a good rapport (or I thought so) with several folks there.
When I had the common rail fuel pump replaced, I had sourced the pump from Denso and Nandi had done the fitting and system coding job. I was expecting the same steps and that is where I was really suprised.
At first the Nandi senior technical leadership denied that the program even existed. When I escalated to the CRM and Toyota, they relented and acknowledged the existence of a Toyota approved program.
Real bomb was a quote of Rs. 25,xxx incl. GST per injector and it would include the labour cost as well.
Denso waz quoting Rs. 17,xxx incl. GST per factory refurbished injector.
So the math worked out to Rs.8,xxx incl. GST per injector as labour and handling. Nandi's excuse was that the premium is needed to cover warranty (Denso provides the said 6 month warranty in the 17K cost) and any other incidental costs. According to the CRM of Nandi, 1KD engines have a lot of rust and can break during opening. I had to try very hard to control the expletives.
The bigger shock was that when I forwarded the quote from Nandi to the Toyota VOC escalation point, they just redirected me to Nandi. I have escalated issues in the past and I've never seen this happen. Toyota must have changed their processes to comply with Indian dealership standards - dealer is king and dealers have complete freedom to fool customers. I wasn't expecting this from Toyota.
When I spoke to the CRM in detail he confirmed that these were Toyota approved rates and that they didn't have any issues if I escalated to anyone in Toyota. And he was right. There was complete radio silence from Toyota VOC apart from a ticket in their system that isn't worth the cost KBs of data that it occupies on a storage.
The whole purpose of the injector refurbishment with Denso was to keep the costs low. A 47% markup isn't exactly low cost of ownership. I agree that this 47% includes labour but the labour for replacing injectors was about Rs. 4-5K the last time I checked.
Takeaways - Toyota India (TKM) is focusing less on its core values of customer satisfaction and quality. I have had multiple instances of Nandi failing to get things right the first time. This time when replacing transmission fluids they followed the procedure of a 2WD vehicle. It was only when I stepped onto the bay and escalated did they followed the procedure of a 4WD. I had asked for cleaning out both the evaporators. After the cleanup, there was something wrong with the rear evaporator and it was letting in foul smells. There are multiple previous instances where workshops are getting procedures grossly wrong. There is no process to focus on these mistakes and work on improvements. Where is first-time-right, RCA or Kaizen?
- Workshops are being given a free hand without much supervision from Toyota. This wasn't the case till a few years back. I loved owning a Toyota because workshops really cared about Toyota's core values
- Toyotas run so well because of the engineering in the design process. They run well in spite of the workshops.
Conclusion
I didn't get the job done for now. I have an option to source the materials and get it done at a reliable FNG. However, considering the amount of time I would have to spend I may still negotiate hard with Nandi and get it done with them. The workshop is close to my place, they have the right tools and I know people on the floor to get the job done right. Even after all this I maintain a great working relationship with the Service manager. He does everything he can to keep me happy. Will I buy another Toyota - I'm waiting for the TNGA-F launch to put my money.
I just got back from a 1,200km family vacation that involved 6 lane expressways, some twisty roads and some very broken sections of road. I still trust my 14 year car to drive respectable speeds on highways, drive through the night and drive over broken surfaces at speeds that most cars wouldn't attempt for the fear of shaking stuff loose.
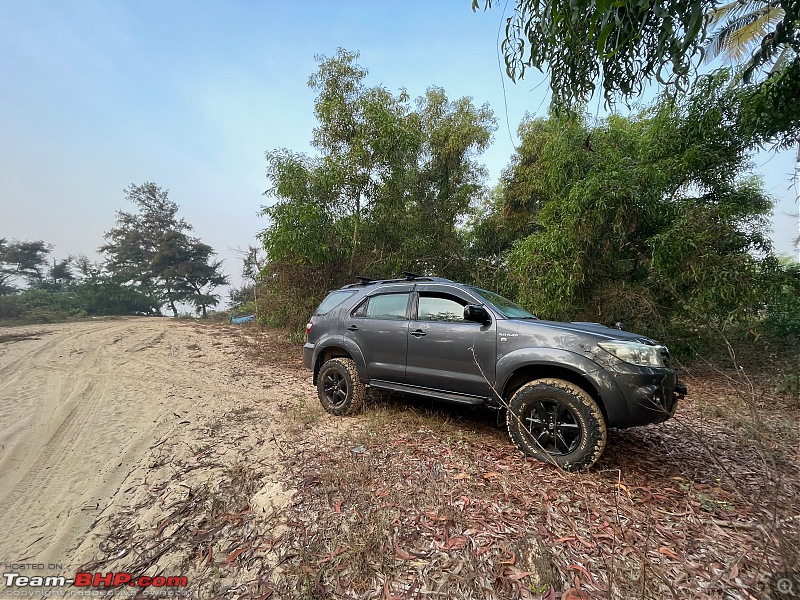