Until the day I test drove the GV, it was not even a contendor in my list. I did it merely to get a reference point. After the TD, it became a serious contendor. That's when I started reading up on it, and that broke the myth that it is a soft-roader like CR-V. And I eventually became a GV owner. Of course, there are still lots of people who believe it to be a soft-roader, hopefully they will be enlightened someday.
However, in the very first month of my Grand Vitara ownership, it became clear to me that I won’t be able to exploit most of its off-roading ability until it has some serious underbelly protection. Probably this is what propagates the soft-roader myth.
GV has one of the flattest underbelly among SUVs.
It has 3 stock skid plates.
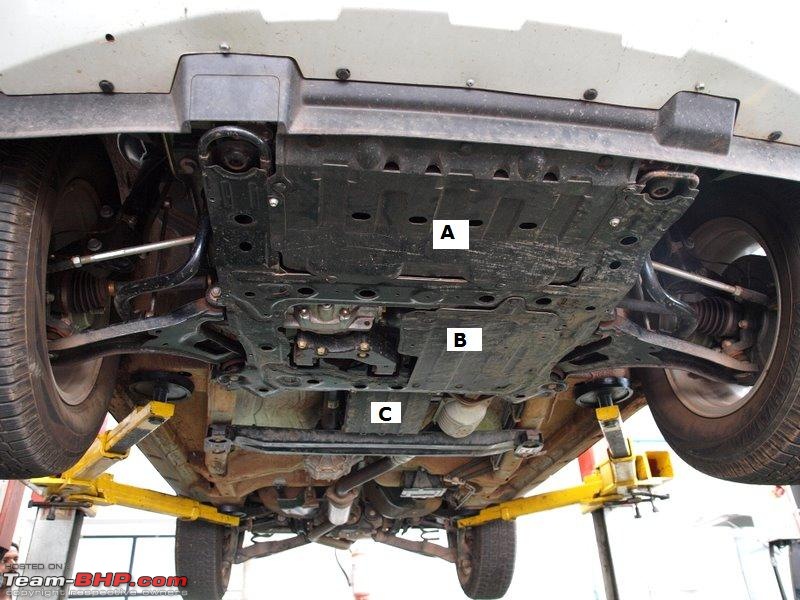
A - Covers (not protect) the engine and radiator
B - Covers the gear box
C - This one is actually silly, it just covers a part of the drive shaft.
The uncovered parts are shown in the next two images. They are mainly transfer case, cat-con, exhaust system, fuel tank, etc.
- Very first week, the transfer case brushed against a protrusion in the mud while trying my first off-roading venture. I had to backup and try a new angle.
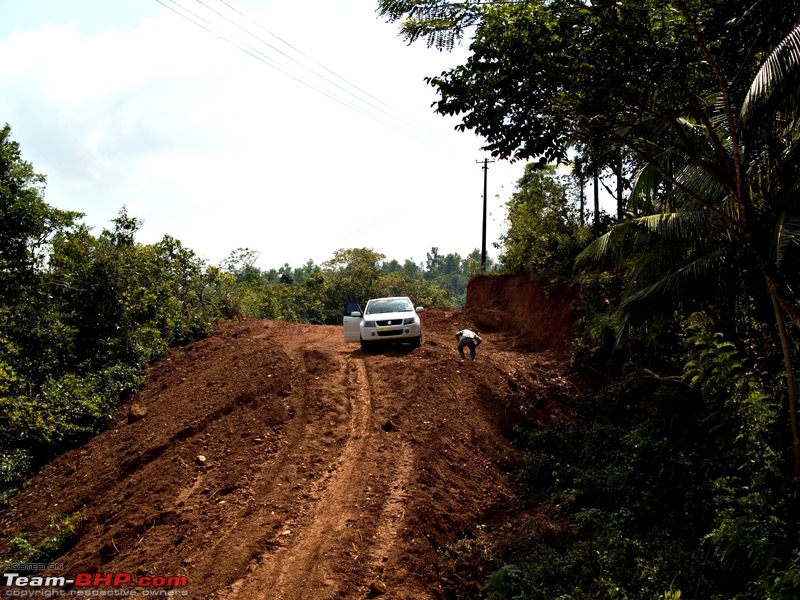
- In a GV photography trip with Rudra, we had to turn back when the road got too rocky for the underbelly.
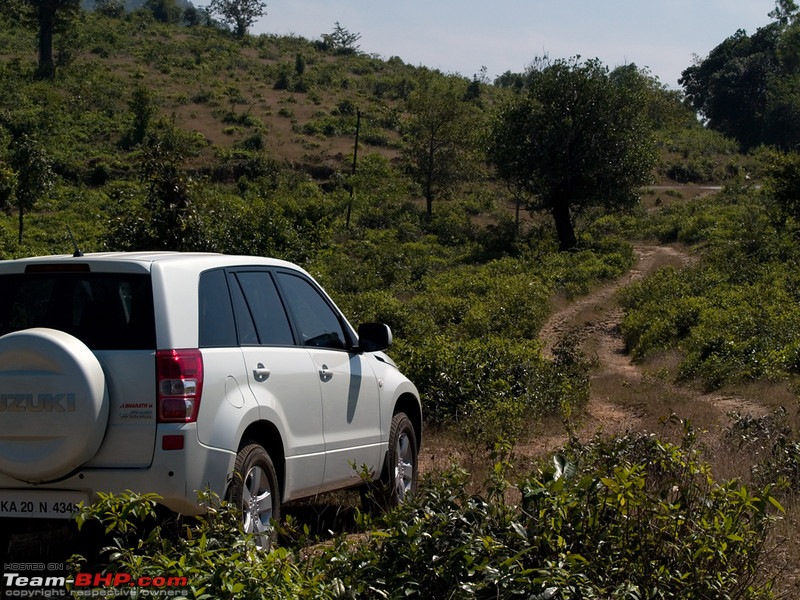
- The Kelambakkam 4x4 off-roading trip finally brought home the point. Offroaders are not supposed to turn back at some rough road, they are supposed ride-on with impunity.
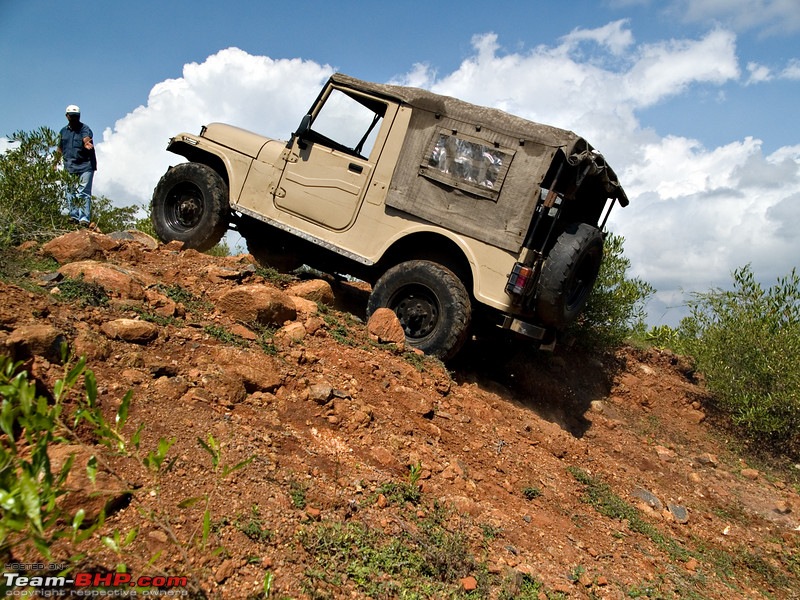
That took me on an extensive research on how get this protection. That is how I discovered the term Skid Plates. I had never heard of it before, but now I needed it. After discussing with many GV owners around the world (in GV forums), one thing was clear. The stock plastic skid plates that come with GV are a joke, most owners who tried off-roading with it, had it torn pretty fast. It was merely a guard against flying debris in gravel road driving, nothing more. After having a first-hand look, I had to concur.
Recently the toughness of GV stock skid plates has been a topic of hot debate. The GV has only 3 plastic skid plates as shown below.
I could bend it using my leg and shoot it at the same time.
Now, I am not at all technical about cars. Until I joined Team-BHP 3 years back, I had never tried to mod any car I owned. Even after joined Team-BHP, I only did modifications that I could understand. Considering my limited automotive knowledge, it never went beyond changing tyres or air filter. So I figured I can do the same with skid plates, buy them and fit them. But it was not so simple this time. Nobody sells off-roading accessories in India, and especially not for Grand Vitara. My research found vendors in Europe and Australia who made skid plates specific to current generation of Grand Vitara. To my surprise, I found that even USA and Canadian GV owners didn’t have ready access to GV skid plates. One Israeli company gave me a quote of US$1400 for shipping it to India, and there is customs duties in addition making it prohibitively expensive. I didn’t get any response from the others; they didn’t want to bother with international shipping.
But it was a learning experience nevertheless; I had learnt that the best option is Aluminium skid plates with 6mm thickness, it is lighter and rustproof. It has to have service holes for various service functions, reducing weight and clearing debris. The best news I heard was that, not a single bolt hole need to be drilled into GV chassis, it has enough readymade bolt holes threaded and non-threaded all across the underbody. It should also allow the chassis to flex as required.
After discussing with many Team-BHPians, and in forums dedicated to off-roading and Grand Vitara, it finally dawned upon me that I may have to consider getting this custom made. I got recommendation on various guys who could do it Chennai, Coimbatore or Bangalore. But they would need my GV for the duration of making it, which would be very impractical, for me. The only practical way would be to get it done locally, within 10Kms of where I live. Now, I live in a small place, where I can’t even get synthetic engine oil or leather steering cover for my GV, I know because I have tried. So, how the heck am I going to get this done?
At first I thought of hiring the aluminium workshop and give him my requirement. But that thought didn’t last long. I have been a product development engineer all my professional life, and it has taught me that one can’t build a product unless one knows the target domain very well. Therefore, the thought of two automobile noobs (me and the aluminium guy) developing an automotive part for an imported SUV just withered away. The design and construction of the skid plates has to be done by somebody understands the automobile in question very well. There are many moving parts down there, the drive shaft, the suspension, and many other things I don’t know about.
Now when I think about it, I don’t remember how it came about. In one of the visits to the local Maruti dealer/service station, Abharan Motors, I ended up discussing this problem with the Works Manager Mr.Nagaraj Kamath. Out of the blue, he offered to look into the matter himself and check out the possibilities. I know him pretty well from before, he was the guy who supervised the Baleno crank shaft issue last year. So, I quickly emailed him all the links on various skid plates available for GV around the world. Soon he got back to me saying this may be something worth trying. Since this was an experiment, I didn’t put any budget or time constraint, and asked him go ahead.
The work got kicked off with the purchase of an 8ftx4ft aluminium sheet of 6mm thickness. It weighed about 50Kgs, although only 2/3 of it might be used eventually. I had to leave the GV couple of times for measurements. After that it took a long time, while they figured out what to cover, what not to cover, how to cover, how not to cover, etc. In fact, it took little over two month when I finally got a call to look over the first draft. The skid plates were supposed to be in 3 parts, and only the first one had been shaped and rest weren’t. It is a good thing that I am from product development, I understood this was only an iteration and I knew why they had to do it one step at a time. Plus, bending the 6mm aluminium to required shape by hand was a major problem. Nobody had access to any hydraulic press capable of doing this. So they had to make channels and bend it along the channel, the channel is later welded close. Meanwhile, it also came to light that Mr.Kamath used to rally-prep Kadur Family rally cars in the 90s. That explained why he was open to take up this experiment.
Initial design
Two weeks later, they were ready for the first fit. Also, we discussed the rear part again and decided to change it. So the design changed from 3 pieces to 5 pieces. Now there was an U-shaped steel bracket to mount the rear skid plates, a bracket that is designed to take load. Usually the middle part of the wheelbase should have maximum clearance, but GV has the unprotected transfer case right there. Although this piece looks as if it is reducing the GC in the center, it is almost at the same height as the exhaust pipe, but protects the transfer case from any direct impact.
Meanwhile, I have to mention that most of the design and implementation was being handled by a senior mechanic named Mr.Ramachandra. This time I left the vehicle for 4 days so that they can have ample time trying it out, I got an Esteem as a loaner car for that period.
Last Saturday they were finally ready with all the skid plates, for field testing. Finally, it was time for me to show the designers what the product was supposed to do. I took both Mr.Kamath and Mr.Ramachandra to my office grounds where I had a pretty good off-roading site. This is the same place where we off-road tested the Gurkha. As I chose the off-road obstacle to test the skid plates, I saw a strange expression on both their faces, and I suddenly realised that they have never seen off-roading of this kind.
All this time they were thinking of roads with rocks or big potholes and not the sport of off-roading.
Notice the normal gap in the front wheel arch.
The front skid plate hits the obstacle, see the wheel arch gap increase.
Now the middle part hits the obstacle, see the wheel arch go up again, it could have been the transfer case.
I climbed the obstacle in 4L easily and they were quite mesmerized at how easy it was in the end. The underbody banged the ground as expected at couple of spots. Mr.Ramachandra was closely watching which parts hit the ground, all of them were on the skid plates and at well supported places.
Here is the animated image of the full test.
After trying it once more, we found similar results. Then I offered to take both of them as passengers on the same ride to see the effect of additional load. This time we hit the ground harder and in many more spots. Again, skid plates took on all the contact. The test was complete, and the result had to wait until we return to the service station. Before returning, I took them to my computer and I showed them the photos from Kelambakkam off-road training. I think they finally understood what I was trying to do and why I needed skid plates so badly.
Back at the service station, we again hoisted the vehicle and carefully scrutinized the effect of the field test. The Skid plates had held their place very well, and had taken the brunt of the hits. No other part had touched the ground. The field test was a thumping success. So the skid plates were removed for finish up. All the steel brackets had to be fully welded and painted in the same process used for painting the chassis, the antirust coat followed with automotive paint. The skid plates had to be further bent at the right places in order to flush with the underbody.
A week later, that is yesterday, was the final installation. I spent nearly 3 hours standing under the GV watching the final installation. It was fun to watch so much excitement by many mechanics and service advisors unrelated to this project either helping out or watching the progress. I found Mr.Ramachandra taking down diagrams and measurements of various parts for his reference. Although this was his design, he had never committed it to paper until today. His enthusiasm and pride towards the project was very apparent.